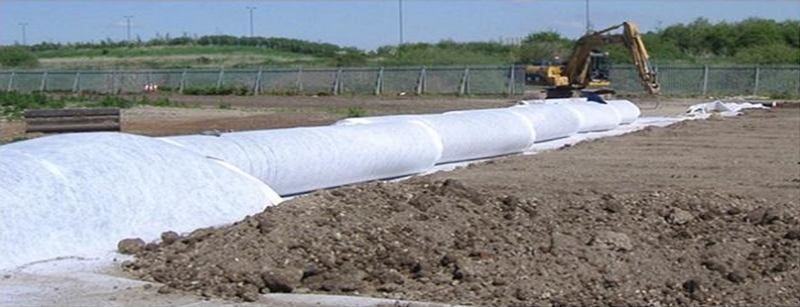
Case Study of Anti-Seepage Engineering in a Landfill Site
Anti-seepage engineering in landfill sites is critical for preventing leachate contamination of groundwater and soil. This study takes a municipal solid waste landfill as an example, systematically analyzing the design, construction, and material selection of its anti-seepage system, with a focus on the application methods of high-density polyethylene (HDPE) geomembranes, geosynthetic clay liners (GCL), and composite drainage nets. The results demonstrate that a scientifically designed anti-seepage system can effectively control pollutant migration, offering significant environmental benefits.
1.Project Background
The municipal solid waste landfill covers an area of approximately 50 hectares, with a designed capacity of 8 million cubic meters and a service life of 20 years. The site’s geology primarily consists of sandy clay, with a shallow groundwater table (about 3 meters deep). To prevent leachate contamination, the project adopted a “double-layer anti-seepage + leachate collection” system, utilizing 1.5mm thick HDPE geomembranes, GCL, and three-dimensional composite drainage nets as core materials.
2.Anti-Seepage System Design
(1) Anti-Seepage Layers
The layered structure from bottom to top includes:
-Base Layer: Compacted natural foundation with compaction degree ≥93%;
– GCL Layer: 6mm thick sodium bentonite pad as a secondary anti-seepage and self-healing layer;
– HDPE Geomembrane Layer:1.5mm smooth HDPE membrane with permeability coefficient ≤1×10⁻¹² cm/s;
-Composite Drainage Net Layer: 3D geocomposite for leachate and gas drainage;
– Geotextile Protection Layer: 600g/m² non-woven geotextile to prevent mechanical damage;
– Cover Soil Layer:30cm thick clay cover for ecological restoration.
(2) Leachate Collection System
HDPE perforated pipes (slope ≥2%) were installed at the base of the anti-seepage layer, connected to a regulating pond. Leachate is treated to meet discharge standards.
3.Key Construction Technologies
- Foundation Treatment: Remove roots and sharp stones, ensuring surface≤2cm/2m after compaction.
- HDPE Membrane Installation:Hot wedge welding with overlap width ≥10cm; double seams tested via air pressure (0.2MPa for 5 minutes with no leakage); – Slope anchorage using “T-shaped” trenches (depth ≥1.5m) filled with concrete.
- GCL Installation: Natural overlapping (width ≥15cm), forming a continuous barrier upon hydration.
- Quality Control:
– 100% spark testing for seams (15kV voltage);
– Random shear strength tests (≥25N/mm²).
4.Implementation Results
– Anti-Seepage Performance: Post-construction tests showed 99.6% weld pass rate and 95% leachate collection efficiency;
– Environmental Impact:COD levels in groundwater decreased by 80% with no contamination spread;
– Economic Benefits: 30% cost savings and 20% shorter compared to traditional concrete systems.
5.Conclusion
This project achieved efficient anti-seepage and ecological restoration through rational material selection (HDPE+GCL+composite drainage nets) and strict construction management, providing replicable technical insights for similar projects.