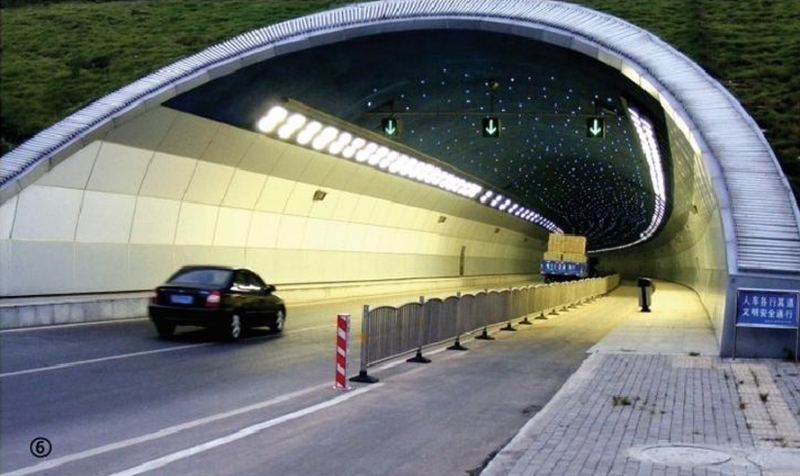
Geosynthetic Innovations in Modern Tunnel Engineering: Materials Revolutionizing Underground Construction
Abstract
With the global surge in transportation infrastructure demands, geosynthetic materials have become indispensable in addressing complex geological challenges in tunnel construction. This article analyzes the cutting-edge applications of geosynthetics in tunnel waterproofing, structural reinforcement, and environmental sustainability, supported by engineering data and case studies.
1. Geosynthetic Materials for Tunnel Engineering
Modern tunnels face three critical challenges:– 45% of structural failures linked to water infiltration
– 30% cost overruns due to unstable strata
– 25% construction delays from traditional reinforcement methods
Key Geosynthetic Solutions:
1.1 Waterproofing Membranes (HDPE/ECB)*
– Thickness: 1.5–3.0 mm
– Peel strength: ≥6 N/mm
– Permeability: <0.1 L/m²/day
– Service life: ≥100 years
1.2 Geogrid Reinforcement Systems
– Polyester/PVC materials
– Tensile strength: 50–200 kN/m
– Aperture size: 25–50 mm
– Creep resistance: <3% after 10,000 hours 1.3 Drainage Composites – 3D geonets + nonwoven geotextiles – Flow capacity: 500–2,000 L/m·min – Clogging resistance: >90% efficiency after 10-year simulation
2. Engineering Applications
2.1 Composite Lining Systems– Primary Support Layer
– Sprayed concrete + glass fiber geogrids (axial stiffness: 1,200 kN/m)
-Waterproofing Layer
– ECB membrane + self-adhesive strips (joint strength: 8 N/mm)
– Drainage Layer
– Geocomposite panels with integrated monitoring sensors
2.2 TBM Tunneling Enhancements
– Geotextile-backed segment gaskets reduce leakage by 70%
– Bentonite-geomembrane slurry walls for soft soil stabilization
– Real-time deformation monitoring using fiber-optic geogrids
3. Case Study: Alpine Base Tunnel (2023)
Project Data– Length: 28 km | Depth: 2,300 m | Overburden pressure: 25 MPa
Geosynthetic Applications
– High-strength PVC-P geogrids (300 kN/m) in fault zones
– Triple-layer HDPE membranes with thermal-resistant coatings
– Automated drainage system (flow rate: 1,800 L/m·min)
Results
– Water inflow reduced from 150 L/s to 5 L/s
– Construction time shortened by 14 months
– Maintenance costs lowered by 40%
4. Sustainability & Innovation
4.1 Eco-Friendly Materials– Recycled PET geotextiles (85% post-consumer waste)
– Bio-based polymer membranes (CO₂ reduction: 60%)
4.2 Smart Geosynthetics
– Strain-sensing geogrids with 0.01% accuracy
– Self-healing membranes (microcapsule technology)
– AI-powered defect detection systems
4.3 Lifecycle Metrics
| Parameter | Traditional Methods | Geosynthetic Solutions |
| Construction Period | 5 years | 3.8 years |
| Energy Consumption | 850 TJ/km | 520 TJ/km |
| Carbon Emissions | 45,000 t/km | 28,000 t/km |
Conclusion
Geosynthetic materials have transformed tunnel engineering into a precision science, resolving historical dilemmas of waterproofing, ground stabilization, and environmental impact. The integration of smart technologies and sustainable materials promises to redefine underground construction standards global
ly, aligning with UN Sustainable Development Goals (SDG 9 and 11).